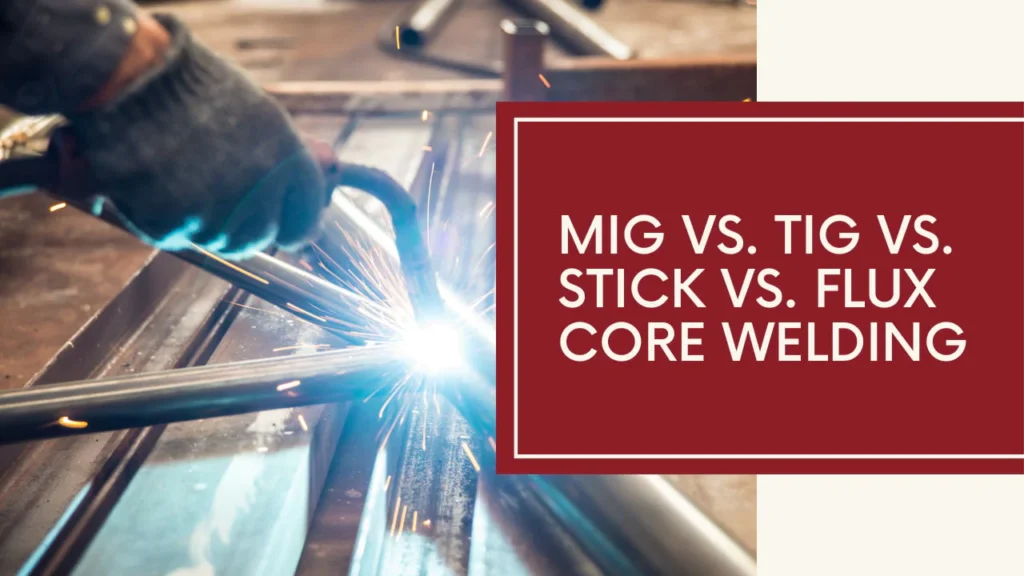
Stick welding, also known as “WeldIT Welding”, is very common among first time welders. Unlike MIG and TIG welding, no shielding gas is needed. This makes it relatively inexpensive to get into and makes it easy to weld in any environment. Whether you’re just learning how to stick weld or you’ve been welding for years, keep these five stick welding tips in mind the next time you strike an arc.
Machine Setup
Make sure your machine is set properly. DIfferent stick welding electrodes are made to weld with different settings. The electrode you’re using, will determine whether you use a DC Positive (DCEP), DC Negative (DCEN), or AC (Alternating Current). Some machines only have the ability to weld in one or two of these modes, so make sure you choose a stick rod that is compatible with your machine.
Each current type will give you different arc characteristics and should be used for different purposes. DC+ is good when you are welding thicker materials, because it gives more penetration than DC- and AC. DC- and AC, inversely, are good when welding thin material due to less penetration at the same amperage.
Now that your machine’s current is set, it’s time to set the machine’s amperage. A good starting point is 1 amp / .001 inches of electrode diameter. This is ONLY a starting point, however, it should get you in the ballpark. You can adjust the amperage up or down based upon your desired arc characteristics from there.
Arc Length is Key
In stick welding few things are more important than arc length. Arc length is the distance between the electrode and the workpiece. Stick welding is what is known as a “Constant Current” welding process. That means, like all CC weld processes, your arc length controls your welding voltage. When you learn to stick weld, it is absolutely essential to learn to maintain a steady arc length. A good rule of thumb is to keep your arc length the same as the diameter of your electrode. If you find that your electrode is getting stuck to the workpiece, your arc length is too short. If you’re getting excessive spatter or undercut, your arc length is likely too long.
Drag your weld
Always pull (or drag) your stick welds. If you try and push your electrode, all you’re going to do is trap the protective slag inside the weld pool, where it will be the opposite of protective. It’ll contaminate your weld instead.
There is only one exception to the drag rule, and that’s when running a vertical up weld. Pushing your weld up a joint is the only time you should ever push your stick weld.
Visibility
Just like with any kind of welding, being able to see what you’re doing is super important. How are you going to run your bead in a straight line or watch your arc distance if you can’t see?
Make sure you’re in a comfortable position where you’ll be able to watch what’s happening. Also, keep your face and helmet out of the fumes. Not only do they limit the visibility of your weld, but they’re harmful to breathe as well.
Clean, clean
Is stick welding the most forgiving when it comes to cleanliness? Yes. Can you just weld over several millimetres of rust with it? No.
While stick welding is absolutely the most flexible when it comes to surface contaminants, even it has its limit. Cleaning your metal is going to give you the best possible weld, so take a few extra minutes to hit your material with a wire brush or a grinder. If you can’t get everything off, that’s ok, but do slow your travel speed if that’s the case. Going slower will leave more time for the gas bubbles to boil out before the slag forms.
Having clean, bare metal to attach your earth clamp to is also a priority because, without a good grounding, you’re not going to get a good weld.
Wet is bad
Generally, electrodes contain some moisture in them, but excessive moisture (or a totally wet electrode) is not good. If you’re using a low hydrogen electrode, then any moisture in your electrodes is a no-no.
If your arc is erratic, wandering or rough, there’s a good chance your electrode isn’t dry. Your flux will also chip off and end up in the weld pool (un-melted) which causes weld defects as well.
There are two ways you can fix this.
The first: prevention. Make sure your electrodes are stored somewhere that is dry and preferably sealed so they stay dry.
The second: an electrode oven. Not to be confused with your kitchen oven. An electrode oven will re-bake the flux coating on an electrode, evaporating any moisture and leaving them ready to weld.
Movement
Running a bead with your stick electrode is pretty simple; it’s a steady, straight line. For the same reason you only want to drag a weld, you don’t want to be circling over the back of your weld pool and trapping slag inside.
If your weld joint is too wide for just a single bead, make a second, third, or however many passes you need in order to properly fill it. These will all be straight lines, with a 50/50 overlap of the filler and base metal to fuse them together.
Travel Speed
A good travel speed is a consistent one. It’s also one that doesn’t burn through your plate or leave your bead sitting on top of the metal instead of melted into it. How can you tell if you’re too fast or too slow?
If you’re moving too fast, you’ll end up with a narrow, high bead that looks like it’s sitting above the metal. That’s because it is, as there wasn’t enough time to heat the workpiece and electrode to have it melt in.
If you’re moving too slow, your puddle will get wider, but the build-up will also be higher, and you’ll have shallow penetration. That’s because instead of melting down, your puddle goes sideways instead, so you get a fat bead with no extra penetration.
Dry runs
Doing a test run for any weld is a good habit to pick up, but it’s especially good for stick welding.
It’s definitely better to find out before you start welding that your elbow is going to bang into the table or another corner or anything as your electrode melts.
Making sure you can move down with your electrode, and you won’t be obstructed means you won’t need any unnecessary restarts halfway through your joint because you suddenly realised you had to reposition.
You always want to be comfortable before starting your weld, and doing a dry run will ensure that you can stay comfortable.