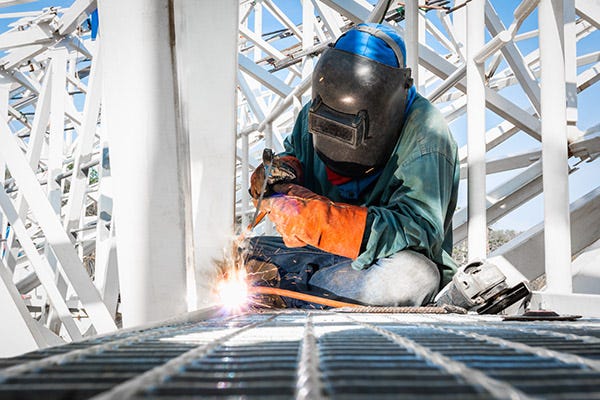
Mastering the Art of 7018 Welding Rod Amperage for Success
Welding is both an art and a science, requiring precision, skill, and an understanding of various factors influencing the process. Among these factors, amperage plays a crucial role, especially when using specific welding rods like the 7018. We will delve into the intricacies of 7018 welding rod amperage, exploring its significance, determining the right settings, mastering techniques, and troubleshooting common issues.
Importance 7018 Welding Rod Amperage
7018 welding rods are renowned for their versatility and strength, making them a popular choice across industries ranging from construction to manufacturing. However, to harness their full potential, welders must master the art of adjusting amperage effectively.
Amperage, also known as current, refers to the flow of electrical charge through a conductor, which, in welding, generates the heat necessary to melt the base metals and filler material.
Role of amperage in welding
Amperage directly influences the heat input into the weld pool, affecting penetration, deposition rate, and overall weld quality.
Characteristics of 7018 Welding Rods
Composition of 7018 welding rods
7018 rods consist of a flux-coated core wire with specific additives, designed to provide stable arc characteristics and produce high-quality welds.
Unique properties of 7018 rods
7018 welding rods offer excellent slag control, minimal spatter, and strong weld bead formation, contributing to superior weld aesthetics and mechanical properties.
Right Amperage for 7018 Welding Rods
Factors influencing amperage selection
Several factors, including electrode diameter, material thickness, joint configuration, and welding position, influence the optimal amperage setting for 7018 rods.
Importance of electrode diameter
Thicker electrodes typically require higher amperage settings to achieve proper fusion and penetration, while thinner electrodes necessitate lower amperage for controlled heat input.
Welding Techniques with 7018 Rods
Proper electrode angle and manipulation
Maintaining the correct angle and steady travel speed is essential for consistent bead formation and proper fusion, ensuring strong and aesthetically pleasing welds.
Techniques for different welding positions
Adjusting amperage and technique according to welding positions—such as flat, horizontal, vertical, and overhead—ensures optimal penetration and deposition, minimizing defects and improving productivity.
Common Mistakes in Adjusting 1/8 7018 Welding Rod Amperage
Overheating and underheating issues
Incorrect amperage settings can lead to overheating, causing excessive spatter, distortion, and weld defects, or underheating, resulting in inadequate fusion and weak joints.
Impact on weld quality and strength
Inconsistent amperage control compromises weld quality and strength, increasing the likelihood of defects, rework, and structural failures, posing safety risks and reducing productivity.
Tips for Mastering 7018 Welding Rod Amperage
Practice with scrap material
Regular practice on scrap metal allows welders to fine-tune their amperage settings, refine their technique, and gain confidence in achieving optimal weld results.
Seek guidance from experienced welders
Learning from experienced welders and seeking feedback on amperage adjustments and welding techniques can accelerate skill development and enhance proficiency.
Safety Precautions During 7018 Welding Rod Amperage
Importance of protective gear
Wearing appropriate personal protective equipment, including helmets, gloves, and flame-resistant clothing, protects welders from heat, sparks, and harmful fumes, ensuring a safe working environment.
Ventilation and fire safety measures
Maintaining adequate ventilation and implementing fire safety protocols, such as fire extinguisher placement and hot work permits, minimizes the risk of fire hazards and ensures workplace safety.
Packaging, Storage, Handling and Reconditioning
Because of the low-hydrogen designation of E7018 stick electrodes, these products usually ship from the filler producer in a hermetically secured plan. To safeguard from dampness damages, it is essential to keep that bundle undamaged till the items are ready for usage. It is likewise crucial to keep the stick electrodes in a completely dry storage space location.
Once opened up, welding operators should handle the stick electrodes with tidy, dry handwear covers to prevent dirt and debris from sticking to the items’ finishing and to get rid of the opportunity for wetness pick-up from the sweat or oils on their hands. These products likewise require to be kept in an oven at the temperature levels advised by the filler steel producer after being opened.
In some cases, particular task codes might determine for how long a stick electrode plan can continue to be open on a jobsite and just how frequently the product can be reconditioned in a holding oven– regular reconditioning can degrade the outer layer and lessen the product’s shelf life. Constantly seek advice from the specs and codes for the demands on each work.